
Unlimited application possibilities:
How our technology empowers you.
Applicationfields
We provide innovative technologies to support companies across a wide range of industries. Discover our tailored solutions designed for your specific applications.
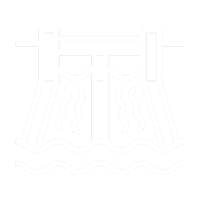
Hydroelectric Power Plants
Inspecting components in hydroelectric power plants presents unique challenges requiring both precision and efficiency. For instance, when examining steel blades measuring an impressive 4.5 meters wide and 3 meters high, our innovative technology dramatically reduced inspection time—from 40 hours with a two-person team to just 4 hours with a single technician.
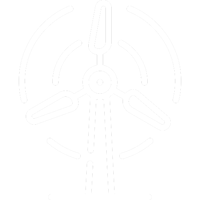
Windfarms
In the wind power industry, inspecting large components like rolling bearing rings, planet carriers, and gear rims with internal and external gearing demands the highest level of precision. Our cutting-edge testing technologies enable fast and efficient evaluation of components with diameters exceeding 13 meters.
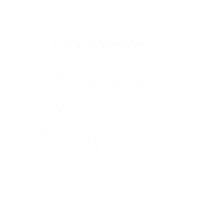
Engine construction
In engine construction, precision and reliability are essential for quality control. Our advanced testing technologies provide fast, cost-effective, and dependable MT testing and demagnetization for critical components, including crankcases, cylinder heads, gears, crankshafts, camshafts, and connecting rods.

Gear manufacturing
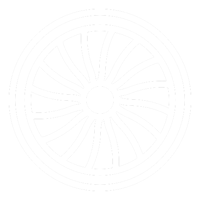
Turbine construction
Managing residual magnetic field strength is critical in turbine construction. For example, after demagnetizing a gas turbine rotor, the maximum residual field strength was reduced from nearly 200 A/cm to less than 3 A/cm—a remarkable improvement in precision and efficiency.
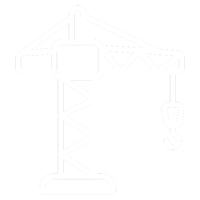
Crane construction
In crane construction, machine and steel components—such as lattice tube masts and welded structures—undergo rigorous quality testing. For example, during MT inspection of a central girder approximately 9 meters long, multiple-meter test sections are examined in a single step, ensuring thorough evaluation of all weld seams in every defect direction.
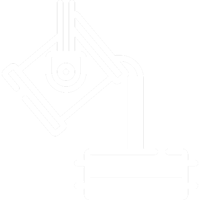
Foundries
Designed for foundry applications, our Multipuls-1003-E3 device features cutting-edge three-pulse technology (3-DC-Pulse Technology), making it ideal for thick-walled, large components with rough surfaces. With its powerful 3 x 30,000 A pulse capability, even the largest cast components can be MT-tested and demagnetized quickly, reliably, and cost-effectively.

Large blower construction
In large blower manufacturing, components such as impeller blades, impellers, spars, and housings undergo rigorous quality testing. The image showcases an impeller blade inspection in its assembled state—a method that minimizes assembly work and saves valuable time by allowing testing directly on the fully assembled component.

Galvanizing plants
In galvanizing plants, our advanced direct current pulse technology enables fast, reliable testing of steel components. Cracks can be accurately detected even beneath zinc layers up to 800 µm thick. This cutting-edge technology ensures the highest inspection precision, maximizing safety and quality.

Forges
In forging shops, components such as rings and shafts are inspected using our advanced DC pulse technology. Forged rings, in particular, benefit from the fast and efficient process, allowing for reliable MT crack testing and precise demagnetization in a single step—ensuring the highest quality standards.
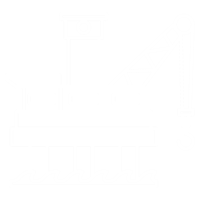
Off-shore
In the offshore sector, high-stress components like elevator links are subject to stringent testing standards. Our advanced direct current pulse technology detects even the smallest defects beneath zinc coatings—flaws that traditional methods, such as hand magnets, often miss.

Aircraft construction
Our MT testing and demagnetization devices play a critical role in aircraft manufacturing, particularly in turbine prototype development. They safeguard sensitive encoder systems from interference caused by residual magnetic fields while also ensuring effective tool demagnetization.
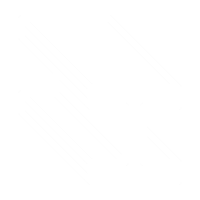
Steel construction
In the steel construction industry, our magnetic particle testing (MT testing) and demagnetization technology are primarily utilized for large, complex components and welded structures. The component shown here is a high-capacity container in which we performed the demagnetization of the nozzles. Due to the presence of strong residual magnetic fields, proper welding would not have been feasible without our intervention.

Pipeline construction
Our Multipuls-1003-E3 device, featuring three-pulse technology (3-DC-Pulse Technology), is perfectly suited for thick-walled and large components in pipeline construction. With a powerful 3 x 30,000 A output, it enables fast, reliable, and cost-effective MT testing and demagnetization, even on rough surfaces.
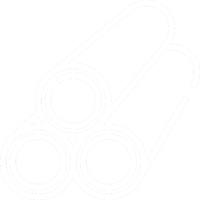
Plant engineering
In pipeline construction, heat exchanger tube bundles are efficiently demagnetized. The image depicts a bundle of 40 heat exchanger tubes, each measuring 27 meters in length, successfully demagnetized in just minutes as part of a large-scale order.

Shipbuilding
Our DC pulse devices are widely utilized in shipbuilding, especially for submarine construction, where long weld seams require precise inspection. This advanced technology reliably detects near-surface defects that conventional AC-powered hand yokes often miss.

Materials testing labs
Our MT testing and demagnetization devices are utilized in materials testing laboratories across Europe, including by esteemed organizations such as TÜV and Dekra. Known for their exceptional precision and reliability, these devices ensure accurate testing of a wide range of materials and components—areas where conventional hand yokes are often insufficient.
From offshore to steel construction:
Our technology overcomes every challenge. Discover what’s possible.